LASER WELDING SYSTEMS
CNC Laser Welding Workstations
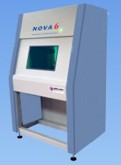
Nova-6 Workstation
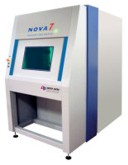
Nova-7 Workstation
MIYACHI EUROPE designs and manufacturers as part of our range of laser welding machines a number of CNC laser welding workstations, which provide a safe working environment for laser welding.
Some of the characteristics of these systems are:
- Modular system which can be customized for specific applications
- Fully integrated PC based controller (IMS-3000), which integrates the laser welder, motion system, data logging and process monitoring
- Highly accurate multi-axis motion systems
- Advanced CNC controller
- CE-certified, laser safe enclosure and workstation
Standard models, Nova-6 and Nova-7
Our most popular workstation is the NOVA-6 which is used in applications ranging from the manufacture of medical implants to sensors, pacemaker leads and research. We also offer a larger version the NOVA-7 which uses a xyz gantry configuration and includes machine vision to weld trays of parts. Both systems are very similar and can be adapted to your specific requirements.
Glovebox Laser Welding Workstations
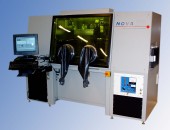
Nova CA Glovebox Laser Welding System
MIYACHI EUROPE is manufacturing two different standard Glovebox Laser Welding systems, used in hermetic seal welding applications such as the production of titanium medical implants or the packaging of military grade electronics. The Glovebox Welding systems are similar to our CNC Laser Welding Workstations, using the same software and hardware, but with the added advantage of welding in an inert environment.
Our glovebox laser welding systems work with our proprietary windows based user interface offering one single application to control not only the glovebox parameters, but also the laser programming, CNC motion and FDA / Mil-spec data logging; and are usually configured with either a three or four axis CNC controlled motion system. Depending on the accuracies required, servo motors or linear motor driven slides are used.
To ensure maximum weld quality we offer special CAM software which generates complete welding programs from CAD files. The weld programs contain tack points, alignment correction routines and weld inspection.
Standard features of our glovebox laser welding systems include:
- Inert welding environment with <1ppm Oxygen and <1ppm Moisture content
- Fully integrated PC controller (IMS-3000), which integrates the laser, CNC motion system and glovebox control
- FDA / Mil spec data logging for product traceability
- Multiple oven configurations
- Accurate 3 or 4 axis CNC motion
- Titanium compatible close loop fume extraction (sooth sucker)
- Single vendor support and service
- Several sizes available with 2, 3 or 4 gloves
- Oil Free vacuum pumps
- Optional turbo pump for high vacuum requirements
- Seamless integration with all Unitek Miyachi Laser Welders
- CE-certified
Turn-key solutions
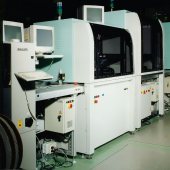
Complete In-line Systems
When our standard workstations don't suffice, we offer complete turn-key solutions, which vary from modified workstations to complete inline automations.
With over 40 years experience in precision joining technology MIYACHI EUROPE are well equipped to deal with many types of automation; supplying and supporting systems all over the world.
Following our true turnkey approach starting with product development, followed by process optimization and ending with the delivery of a manufacturing system, we provide full proof solutions to our industrial customers. Having detailed knowledge about laser welding, lasers and automation enables us to take care of the full project.
All MIYACHI EUROPE automation projects are run according to our ISO-9001 procedures ensuring optimum support and quality to the customers.
This experience in turn-key automation includes technologies like:
- Vision directed motion
- Inline automation
- Semi-automatic turn-table or linear slide based systems
- Automation inside glovebox systems
- Automatic part handling (feeders, pick and place robots)
- Advanced tooling and tool changers
- High speed accurate CNC motion
- Manufacture of modules or production cells which integrate into an automated line